Product Overview
GRAFSHIELD™ GRI™C and GRI™CC insulation panels feature GRI™ insulation with carbon fiber composite (CFC) facing on one or both sides. The CFC face sheet provides superior impact and abrasion resistance, ensuring longer product life in harsh environments. These products are designed for use in high pressure gas quenching processes as well as other applications that require a high degree of protection for the insulation component.
Applications
@ Vacuum furnace insulation
@ Inert atmosphere furnace insulation
@ Inert atmosphere process equipment insulation
@ Semiconductor crystal growing furnace insulation
Features:
@ GRI
TM Insulation Layer;
@ Excellent impact and abrasion resistance
@ Machinability
@ Panels available machined to print
Benefit:
@ Superior energy efficiency and consistent thermal performance
@ Long product life in harsh furnace environments
@ Panel features are easily tailored to customer requirements
@ Customized insulation packages with optimal material utilization
@ Tailor-made panels arrive ready to install
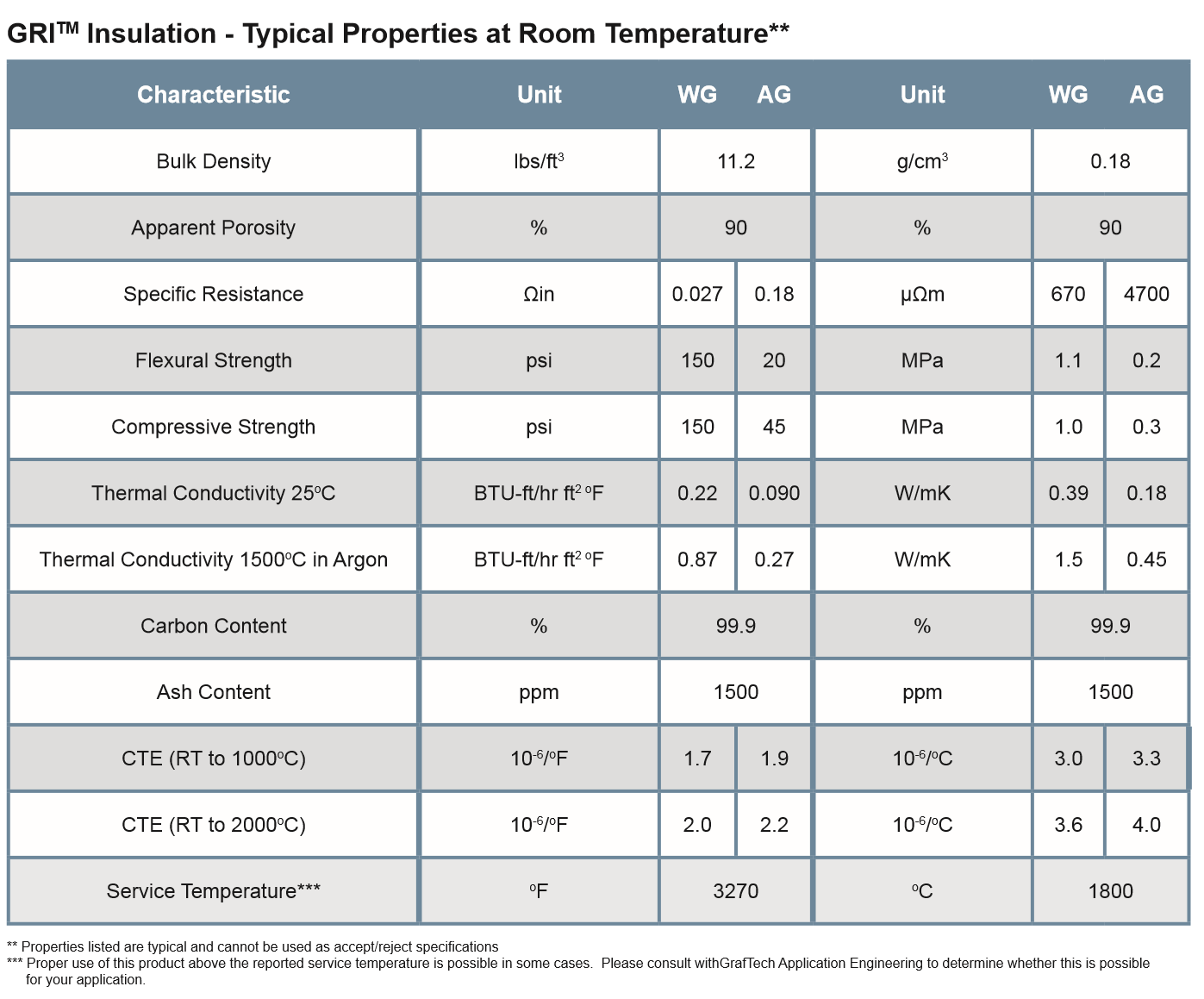
CFC can function at much higher high temperatures (>2400°C) than most other structural materials, owing to its near-100% carbon composition. However, it is similar to other carbon and graphite materials in that it will convert to carbon dioxide in an oxidizing environment as the temperature nears 500°C. Nitrogen, argon, and vacuum environments are suitable.
Rigid insulation with CFC facing has several unique advantages as compared to other insulation products.
One of the most important for current applications is abrasion resistance. While bare insulation and graphite foil-faced products are soft and easily abraded, CFC materials are hard and abrade more slowly. This is a critical feature for insulation panels used in vacuum furnaces for high pressure gas quenching applications. During the quenching step, an inert gas (typically nitrogen, argon, or helium) is introduced into the furnace at pressures up to 20 bar. The gas quickly abrades insulation panels if they are not adequately protected. A key property of CFC is its impact resistance. The insulation in a furnace can be subjected to a variety of inadvertent impacts. These can take place during loading, unloading, and maintenance of the furnace. Regarding quenching processes, parts of the furnace payload can become entrained in the high-velocity gas and collide with the furnace wall. This can easily damage an insulation panel if it is not designed for impact resistance.
Another important feature of an insulation panel with CFC facing is that it provides a high degree of abrasion and impact resistance while
costing customers little space relative to an unprotected panel. A typical CFC facing has a thickness of 0.5 mm. Therefore, furnace users can experience the benefit of long product life without having to increase overall furnace size, decrease hot zone volume, or sacrifice energy efficiency (by making the insulation component of the panel thinner). This is particularly important when replacing old insulation during furnace maintenance or refurbishment.
Rigid insulation panels with woven CFC facings can be expected to deliver long product life in a variety of furnace environments. This is due to the intrinsic properties of CFC, most notably its abrasion and impact resistance. The CFC facing is quite thin, allowing these panels to deliver the same thermal performance as unfaced products with an equivalent form factor.
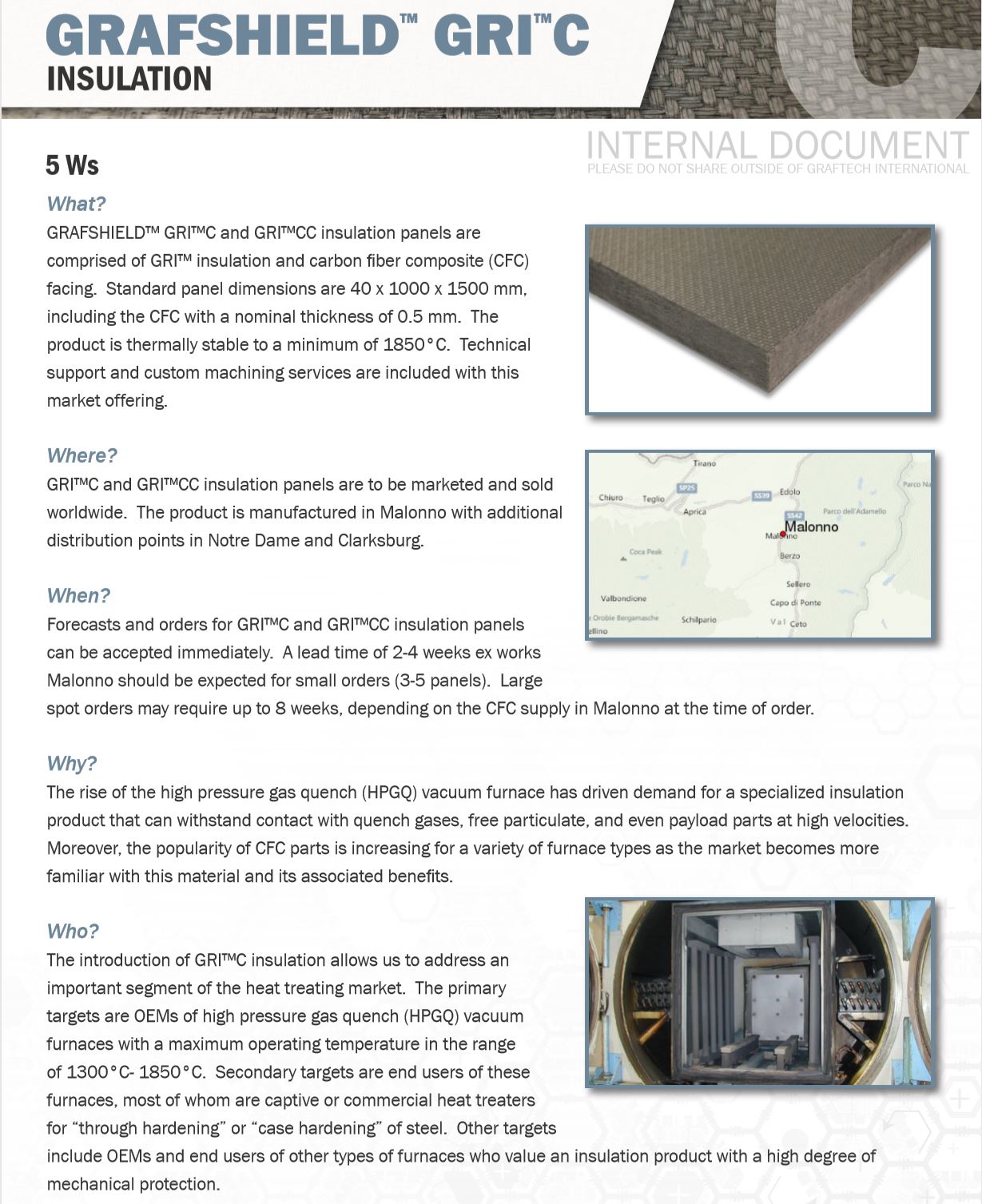